By Valentin Raschke, application engineer, Portescap |August 29, 2023
Searching and selecting a motor for a specific application can often be a challenging task, as there are many potential factors that must be taken into consideration. These include the application’s required voltage, maximum current and diameter, speed, efficiency, and power, among others. Balancing these considerations with other unique application requirements will help ensure the selection of the ideal motor, which is why a collaborative approach between the motion solution and design engineering teams from the outset is vital. R6 2rs
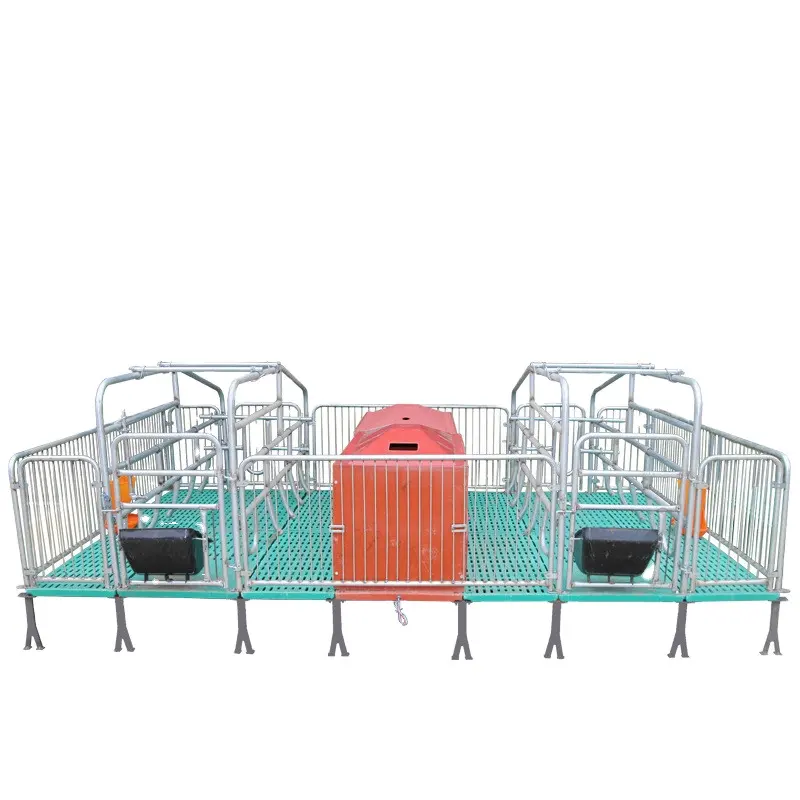
When first approaching a miniature motor supplier for assistance in the motor selection process, one of the initial questions that must be addressed is the application’s specific working point, or the application’s torque and speed. Understanding the load on the motor will help pinpoint the necessary motor power and the required motor accessories. It is also vital to discuss how the motor is integrated into the application, as different types of loads will have a significant impact on a motor’s lifetime and reliability or on the required motor design.
We will explore torque load, radial load, and axial load, which are three different types of loads that are present in common miniature motor applications. We will also highlight why these loads are crucial to the motor selection process.
Torque is the amount of rotational force generated by a motor during its operation. As the purpose of a motor is typically to convert electrical energy (Pelec = voltage x current) into mechanical energy (Pmech = torque x rotational velocity), torque load is present in almost any application for rotary motors.
In most cases, simply selecting a motor based on the required torque value “x” won’t be sufficient. The required torque (and velocity) in an application must be understood over the entire motion cycle, as the motor needs to provide the necessary mechanical power without overheating. This means that you will often be asked by the motion supplier to provide the exact motion cycle that the motor is expected to undergo; this allows for the analysis of the maximum temperature the motor can reach before overheating.
Keep in mind that selecting the right motor requires not only under- standing the required torque value, but also the torque/speed profile over an entire motion cycle and its duty cycle.
In certain applications, the motor or gearbox must not only provide a certain torque to drive the load, but must also support a radial load, which is a force that is acting radially on the motor shaft. One example of this is a belt drive, which is used to drive an axis parallel to the motor. The tension force must be considered as a radial load acting on the motor shaft, especially if the belt is pre-stressed.
Radial load is relevant to motor selection due to its impact on bearing options. In the example of a brush DC or stepper motor, there are two standard bearing options: sleeve bearings or ball bearings. Sleeve bearings typically support a lower radial load than ball bearings, as well as provide a lower lifetime; this is offset by their lower cost. Depending on the total cost of the motor, using two sleeve bearings instead of ball bearings can decrease the cost of a motor significantly. However, for applications like the belt drive and diaphragm pump where a radial load is present, utilizing at least one ball bearing for the front bearing of the motor helps ensure a reasonable lifetime and is thus a better choice.
In contrast are brushless DC motors, which typically use two ball bearings, as they can be driven at much higher speeds compared to DC or stepper motors. A motor manufacturer will recommend a maximum radial dynamic force at which a minimum lifetime of the motor at a specific speed can be achieved. The maximum radial dynamic force will depend on the size of bearings used, the distance between the two ball bearings in the motor, and the position where the radial load applies. A long motor with oversized ball bearings typically supports a larger radial load than a shorter motor.
There are two types of axial loads: dynamic axial load and static axial load.
If an application requires a 90° rotation of the rotating movement at a lower speed, a worm gear can be an ideal solution. A worm gear consists of a worm shaft that features a spiral thread and is driven by the motor. The worm shaft drives the worm wheel with a reduction ratio as small as roughly 2:1 or larger. Following the spiral thread on the worm shaft, a radial and axial load must be supported by the motor.
Sleeve bearings are not meant for supporting significant axial loads; this means that equipping the motor with ball bearings is often mandatory. Similar to the radial load, the maximum recommended dynamic axial load of a motor will depend on the ball bearings and preload used, the distance between the two ball bearings in the motor, and the lifetime requirement.
In the example of a typical axial brushless DC motor design, the dynamic axial load is supported by the front ball bearing, as the inner diameter of the bearing is bonded to the motor shaft. In case of an axial push load acting on the motor, the preload on the front ball bearing is reduced; this can lead to additional radial play, negatively impacting the lifetime, vibration, and noise of the motor. In the case of an axial pull load, the load is acting in the same direction as the internal preload, increasing its stress. Motor manufacturers will usually restrict the recommended dynamic axial load to a certain limit that can be supported by a bearing without negatively impacting its lifetime.
Keep in mind that depending on its direction, a dynamic axial load impacts the motor’s bearing assembly differently. In cases of excessive axial loads above the recommended specification, the bearing assembly or the bearings themselves must be improved.
Besides a dynamic axial force acting on the motor during its operation, there’s also a possibility that at least once during the motor’s lifetime, a static axial load will be applied to the shaft. This is usually the case when an additional component (for example, a pinion) is press-fitted onto the motor shaft of the assembled motor. Shock loads, such as when the motor is used in a handheld device and is dropped on the floor, are another example where static axial loads can occur.
In the example of a motor equipped with ball bearings, the recommended limit for a press-fit operation is typically much higher than for a dynamic axial load. In fact, the limiting factor is only the ball bearings’ elastic limit. As long as the static load applied to the bearing is below its elastic limit, there will be no permanent deformation of the bearing balls or raceway. However, in the same vein, exceeding the maximum recommended load could lead to permanent deformation of the bearing balls and raceway, resulting in reduced life and increased noise and vibration of the bearing.
An additional difference to consider is whether the shaft of the motor can be supported during press-fitting. Certain motors are closed or are equipped with an encoder on the back side, which prevents access to the motor shaft. Without support, the force applied during the press-fit is directly transmitted to the front ball bearing, whose inner raceway is usually bonded to the motor shaft to absorb the axial loads. Supporting the rear shaft allows for a higher force during press-fitting, as the flow of force is going through the motor shaft, not the bearings.
We have reviewed a selection of applications and examples where other forces, in addition to the torque load that is normally present, are acting on a motor. The most common of these are radial and axial loads, which must be taken into consideration in relation to their impact on the motor and how they subsequently influence the selection process of the motor. A dedicated motion solution provider supports customers in correctly capturing the full picture of the loads experienced by the motor in a given application and is therefore fully equipped to develop the most suitable motion solution that fulfills (even exceeds) the application/device requirements.
This site uses Akismet to reduce spam. Learn how your comment data is processed.
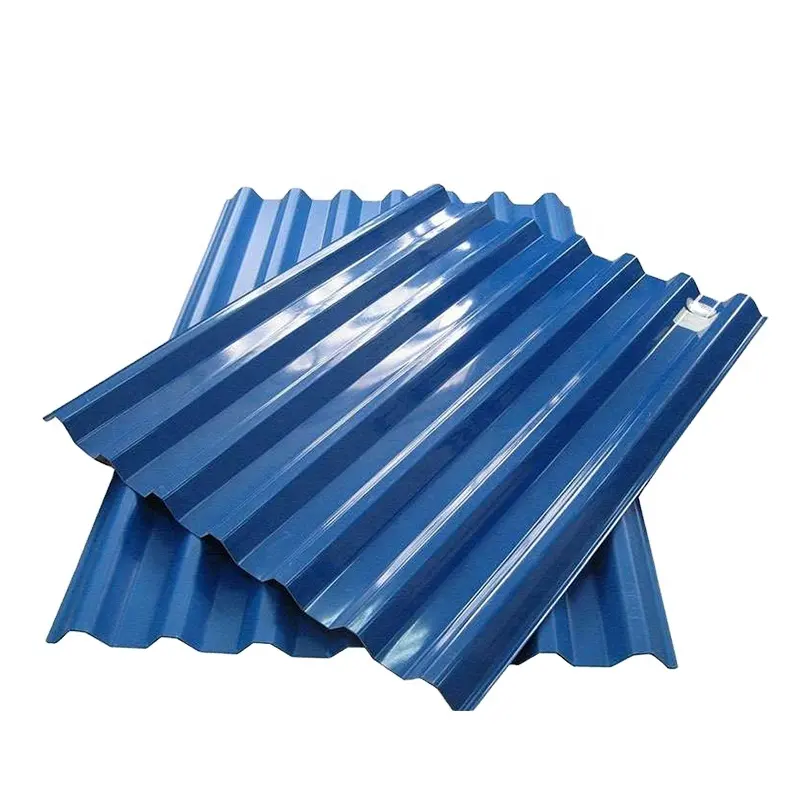
C02 Laser Cutter Copyright © 2023 WTWH Media LLC. All Rights Reserved. The material on this site may not be reproduced, distributed, transmitted, cached or otherwise used, except with the prior written permission of WTWH Media Privacy Policy | Advertising | About Us