We use cookies to enhance your experience. By continuing to browse this site you agree to our use of cookies. More info.
The difference between an abrasion-resistant steel plate and an ordinary steel plate is very important, yet the differences between AR500, AR450, and AR400 are more subtle. In this article, the production of abrasion-resistant steel plate is described and the differences between hardness levels are studied. Welded Stainless Steel Pipe 316l
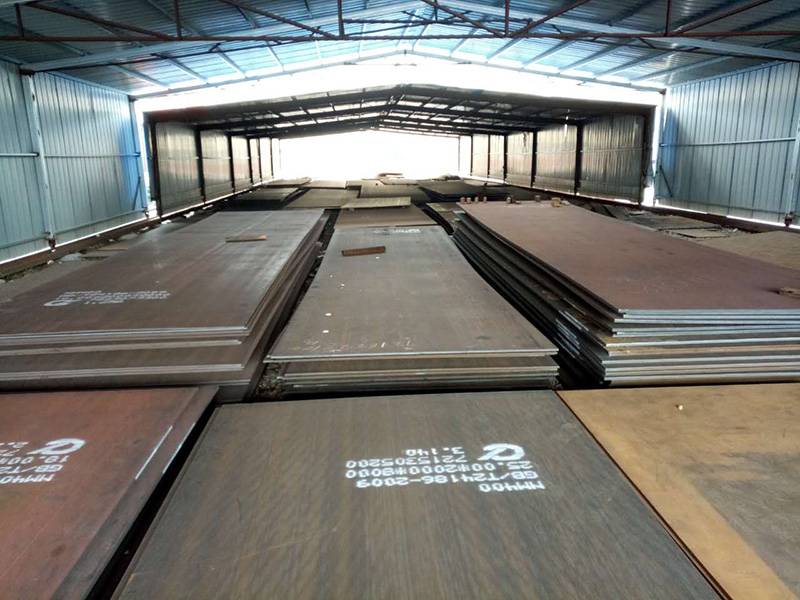
In fabrication and construction, the composition and grade of the steel plate materials used have a tremendous effect on the end product. Abrasion-resistant steel plate is a normal steel plate that possesses a tougher, harder quality that lasts about four times longer when compared to a common high-strength structural steel plate.
However, what makes it tougher, and how doe you know when a project needs abrasion-resistant steel?
Leeco Steel gets this question frequently, so this article provides the run-down on the abrasion-resistant steel plate, and also the differences between hardness levels of AR400, AR450, AR500, and beyond.
Abrasion-resistant (AR) steel plate is a high-carbon alloy steel plate, which signifies that AR is formable and weather-resistant due to the added alloys, and harder due to the addition of carbon.
Carbon is added during the formation of steel plate which considerably increases hardness and toughness, but reduces strength. Hence, the AR plate is employed in conditions where wear and tear and abrasions are the main causes of failure. The AR plate is not perfect for structural construction applications, like support beams in buildings or bridges.
Common applications of the AR plate include dump liners, grates, buckets, construction attachments, conveyors, body armor, and ballistic plates (and as targets at shooting ranges).
AR material is created by quenching and tempering forged steel blocks, or ingots. At the time of this process, the grain structure is modified to increase toughness and promote formability (or, to be less brittle), which leads to through-hardening of the material.
Quenching and tempering (Q&T) is a two-part process:
Quenching occurs when steel is brought to a high temperature, normally between 1,500 and 1,650 °F and is quickly cooled with water. This process allows crystal structures to form within the steel, increasing hardness.
Tempering is the process of re-heating quenched steel to a below-critical temperature (approximately 300 — 700 °F), and then enabling the plate to cool in normal air temperatures.
The reheating of material disintegrates the crystal structures formed at the time of the quenching process, while the long cooling enables the crystal structures to reform — preserving most of the hardness and strength, but increasing the overall ductility.
Usually, abrasion-resistant steel is termed “AR450F” and “AR400F” (and at times “AR500F”). At present, the AR material with or without the “F” is interchangeable, but — traditionally — material with an “F” simply implied that it was "formable" and can possibly be bent to a certain degree without cracking.
When mills created both non-formable and formable steel plates, formable was somewhat costlier. Yet, more competitive pricing and reduced demand have resulted in the production of formable-only AR steel.
AR steel is usually explained as being through-hardened, but what does that actually mean?
The composition of the whole plate changes when the grain structure changes during the primary heating stage of Q&T. This is known as through-hardening. Through-hardening is different from “case-hardening,” also known as “surface-hardening,” which only hardens the surface while enabling the metal deeper beneath to stay soft. In this case, the hardening or composition of the plate only varies at the surface level.
Before this article dives into the difference between these common types of AR steel, it is significant to explain that AR steels are not controlled by a particular chemistry, but by a level of hardness.
A variety of mills may have different “recipes” for AR steel, but the produced material is subjected to a hardness test — called the Brinell Test — for determining the class in which it falls.
The Brinell Hardness Number (BHN) is the technical difference between AR400, AR450, and AR500. BHN signifies the hardness level of the material:
AR600: 570-625 BHN Typically (less common, but available)
Therefore, what does this mean in terms of usability? How do you know which level of hardness the project requires?
Projects that need AR materials are usually those that require a precise balance between brittleness and hardness. As hardness is increased, brittleness is also increased, making the material hard to form, weld, and shape. For some projects, hardness is crucial, and therefore brittleness is compromised; however, in other cases, the material should be formed and handled, so the level of hardness should be decreased.
As a general rule, AR450 and AR400 are the “sweet spots” in terms of good formability combined with good hardness. AR500 and AR600 will last longer and need to be replaced less often for projects that actually beat up the material.
Eventually, the customers and their team will be the best judge of which material is required for their project. Obviously, cost becomes an important factor, as sometimes it is worth having a formable material that has to be changed more frequently.
This information has been sourced, reviewed and adapted from materials provided by Leeco Steel, LLC.
For more information on this source, please visit Leeco Steel, LLC.
Do you have a review, update or anything you would like to add to this article?
In this interview, AZoM speaks to Bruker Optics about the different ways IR light can be used in semiconductors.
At The Greener Manufacturing Show 2023, we spoke with KUORI CEO and Founder Sarah Harbarth about the growth and ambitions of the company as it develops its novel materials.
In this interview, AZoM talks to Geoff Downing and Mark Mattison from Thermo Fisher Scientific and Entegris, respectively, about semiconductors and their importance, manufacture and how gas analysis factors into these processes.
When it comes to powder permeability and powder processing, understanding the permeability of powders is important for pharmaceuticals, food production, and additive manufacturing.
Analytik Jena’s compEAct provides reliable determination of sulfur and nitrogen in liquid, gases, and LPG samples.
Durr’s CR 35 NDT is a portable digital X-Ray computed radiography scanner that is ideal for a wide variety of applications.
The global semiconductor market has entered an exciting period. Demand for chip technology is both driving the industry as well as hindering it, with current chip shortages predicted to last for some time. Current trends will likely shape the future of the industry, which is set to continue to show
The primary distinction between graphene-based batteries and solid-state batteries lies in the composition of either electrode. Although the cathode is commonly changed, carbon allotropes can also be employed in fabricating anodes.
In recent years, the IoT is rapidly being introduced into almost all sectors, but it has particular importance in the EV industry.
AZoM.com - An AZoNetwork Site
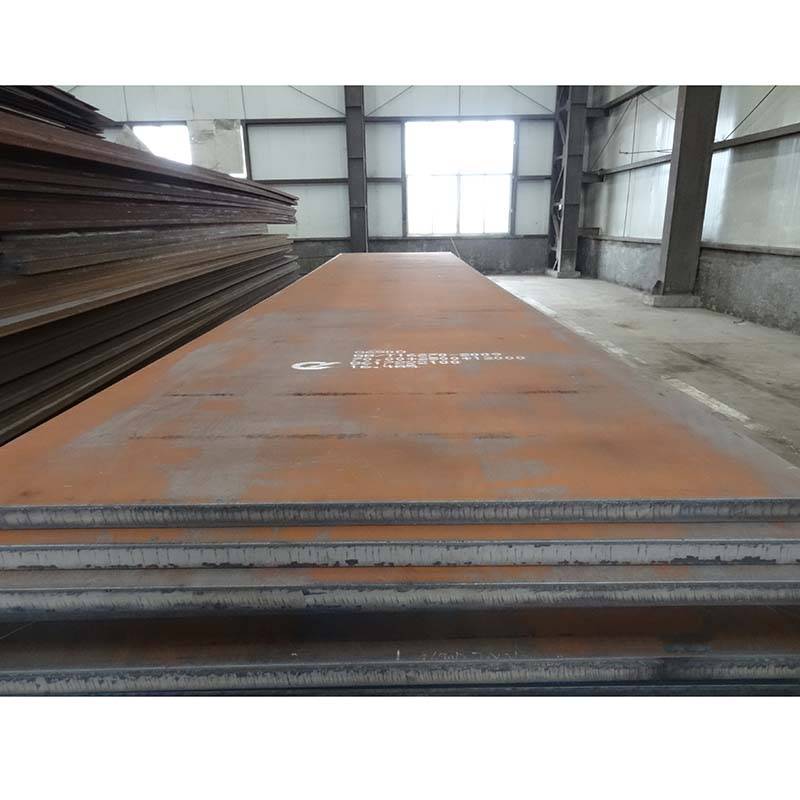
Nm400 Wear Resistant Steel Plate Owned and operated by AZoNetwork, © 2000-2023